~Readymix concrete
Fillmix
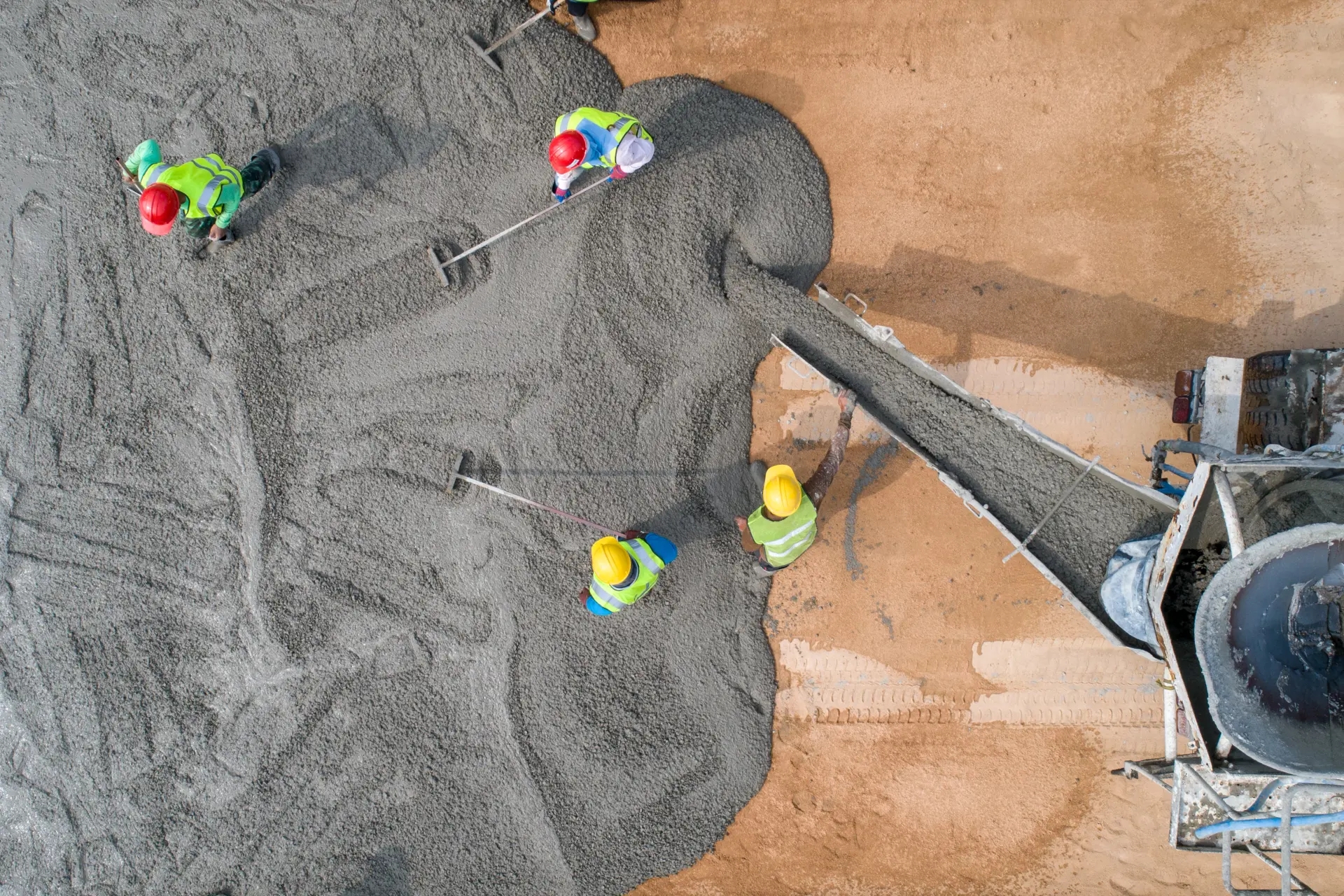
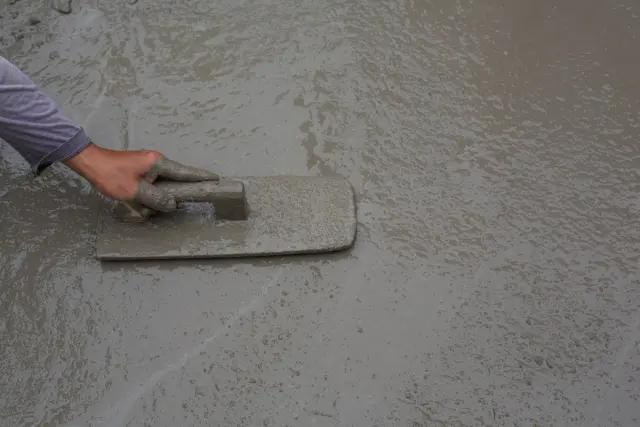
FILLMIX
Fillmix is a non-structural pumpable lean concrete with higher workability and easy to place, used for filling areas.
- Easy to pump
- Faster execution, replacing the conventional system of backfilling
- Minimum or no compaction required
- Minimum manpower required for placing, compaction, tempering, and watering compared to other filling materials like soil, sand, etc.
Application Areas
- Back filling, trench filling
- Used as PCC of foundation base for buildings and pavements
Technical Specifications
- Compressive strength (28 days): 2 - 5 Mpa
- Slump at site: 100 to 150 + mm
- Density: 2000 to 2300 kg/cum
Great Experience in building
Frequently Asked Questions
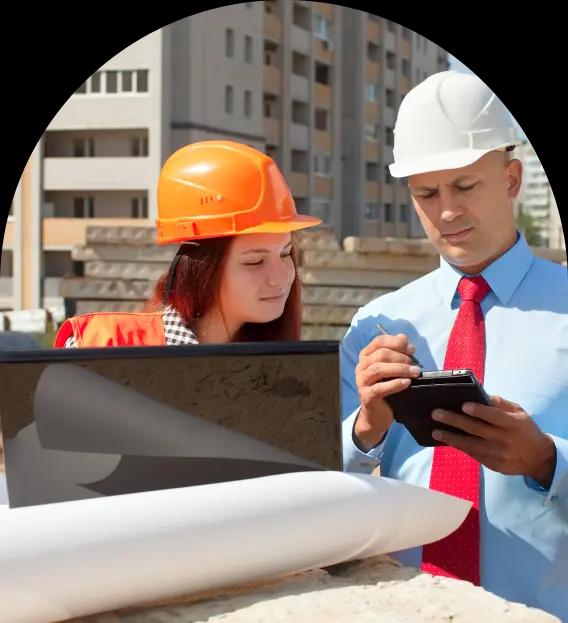
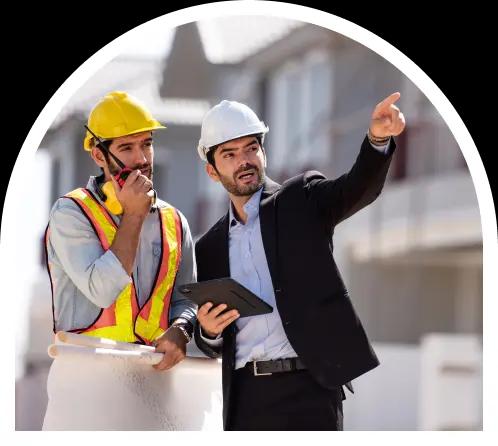
Can't find what you're looking for? Check our FAQ section first. We've compiled answers to the most common questions and concerns our users have. This way, you can quickly get the information you need without having to wait for a response.
Readymix Concrete (RMC) is a pre-mixed concrete that is manufactured in a batching plant or factory according to a set recipe and then delivered to a construction site in its freshly mixed state.
RMC offers benefits such as consistent quality, time savings, reduced labor requirements, precise mixture control, and the elimination of on-site storage and waste.
Quality in RMC is assured through rigorous testing of raw materials, regular plant inspections, adherence to mix designs, and compliance with relevant industry standards.
RMC is suitable for a wide range of construction projects, including residential buildings, commercial structures, bridges, dams, and infrastructure projects.
Many RMC producers focus on sustainable practices, incorporating eco-friendly materials, optimizing energy use, and reducing waste to minimize the environmental footprint of their operations.
The shelf life of RMC is typically limited to a few hours, and it is crucial to use the concrete promptly after delivery to ensure optimal performance.
Yes, RMC can be customized based on project specifications, including strength, durability, and other performance criteria.
RMC producers adhere to strict safety protocols in plant operations and during transportation. This includes regular equipment maintenance, employee training, and compliance with safety regulations.
While RMC is commonly used in large projects due to its efficiency, it can also be cost-effective for smaller projects where the benefits of consistent quality and time savings are valued.
The slump is controlled by adjusting the water and admixture content in the mix. It measures the consistency and workability of concrete; a higher slump indicates a more fluid mix.
Yes, RMC can be formulated to withstand various weather conditions, including hot and cold temperatures. Specialized mixes may be designed for extreme environments.
RMC eliminates the need for on-site concrete mixing, reducing construction time. It ensures a consistent quality mix, speeding up the construction process.
Admixtures are used to enhance specific properties of concrete, such as setting time, durability, and workability. They are carefully selected based on the desired characteristics of the final mix.
The strength of RMC is determined through compressive strength tests. Mix designs can be adjusted to meet the specific strength requirements of different construction applications.
Proper “Delay Finishing & Early curing “procedures, protection from extreme weather, and adherence to recommended placement practices are essential precautions to ensure the desired performance of RMC.